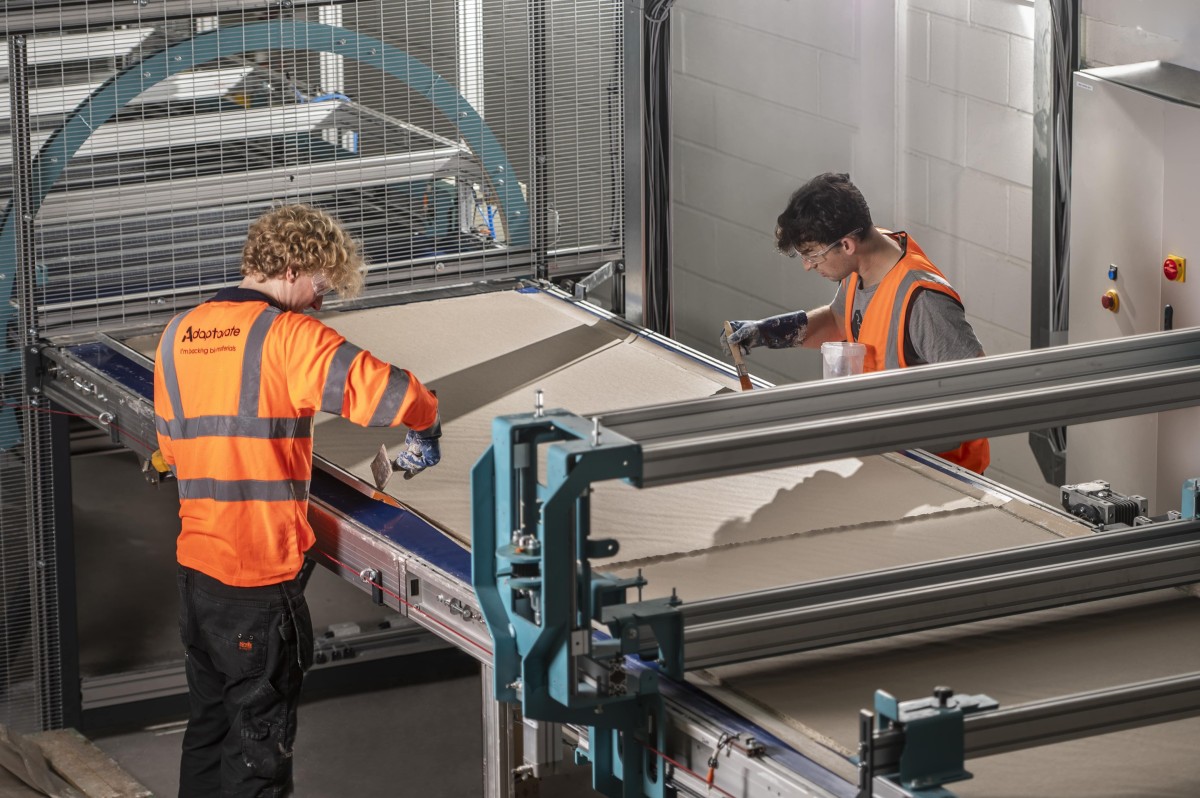
Adaptavate is a world leader in developing low-carbon and carbon-negative construction technology
Breathaboard is Adaptavate’s revolutionary carbon sequestering alternative to plasterboard and can save approximately. 4kg of CO2/m2 in a market of around 13bn m2
The UK-born company has signed pilot projects with companies such as Unusual Rigging and plans to license its technology to global manufacturers to enable low-carbon and carbon-negative construction materials anywhere
Adaptavate, a world pioneer in developing and industrialising low-carbon and carbon-negative construction materials, announces the successful build and commissioning of the world’s first pilot line capable of producing Breathaboard in a continuous, integrated, and scalable process.
Breathaboard is a revolutionary bio-based, carbon sequestering alternative to one of the most widely used construction products, plasterboard. It is produced, specified and installed in the same way but with carbon and performance benefits. Breathaboard saves approximately 4 kg of carbon dioxide per square metre over gypsum plasterboard, so it’s easy to see how quickly a significant difference can be made from a total annual market of around 13bn m².
Adaptavate’s patented technology enables CO2 savings through product formulation and production processes. The company uses fibrous and cellulosic by-products from food and fibre crops and binds them with minerals and small amounts of water to form a flat board material. Unlike other board materials, their production process requires no natural gas and absorbs low concentration CO2, potentially from industrial emissions in the industrial curing process.
Jeff Ive, CTO at Adaptavate, says: ‘The commissioning of our pilot line is the culmination of a year’s hard work from the team. From conception, we knew that for the technology platform to have the impact the planet requires, the solution needed to be scalable! Now that we see full size boards made on a continuously extruded process, with a comparable performance to the incumbent, we can see this vision becoming a reality. The pilot line capability, as part of the development centre, gives us the foundation to replicate our core innovation for production partners around the world, with the confidence that the product is technically scalable. It’s a game changer for us, for our industry, and for the planet.’
Breathaboard production is already oversubscribed until the end of the summer with pilot projects coming to life imminently. Unusual Rigging HQ is the first company using the boards coming from this world’s first pilot line, helping Adaptavate accelerate their development and pilot programme. ‘Adaptavate really is rethinking and redesigning the way building materials are produced, used and disposed of and their commitment to preserving our fragile ecosystem through innovative technology and manufacture aligns strongly with Unusual’s values,’ says Unusual MD, Tom Harper.
Adaptavate is now working with the British Board of Agrément (BBA) and is on track to achieve the BBA Agrément Certificate for Breathaboard, the UK’s first carbon sequestering alternative to plasterboard.
Also, to achieve the greatest level of ecological impact as quickly as possible, Adaptavate’s next step will be consolidate global partnerships to scale its unique technology with the world’s largest construction products manufacturers. This will enable the manufacture of low-carbon and carbon-negative construction materials anywhere in the world, using locally available resources and absorbing CO2 created locally.
Tom Robinson, founder and CEO at Adaptavate, says: ‘This milestone is a step forward in our journey to lead the desperately needed carbon change in the construction industry. It has validated our technology and industrial process to produce a revolutionary alternative to plasterboard. We are now looking to deploy our unique platform in partnership with world leading production companies looking to produce multiple low-carbon and carbon-negative construction products with different value propositions for global markets. Thanks must go to all our funding, technology and product testing partners – this is just the beginning of our transformative industrial approach to a better way of doing business.’
Adaptavate’s overall aim is to be a leader in helping decarbonise the construction industry.
Adaptavate’s pilot line project has been funded by two UK Government grants (Innovate UK), and a group of climate-focused investors dedicated to accelerating carbon removal within the construction industry, such as Counteract, Low Carbon Innovation Fund 2 (LCIF2), Perivoli Innovations and SEMIN Group.
ABOUT ADAPTAVATE
Adaptavate is a world leader in developing and industrialising carbon-negative construction materials. We commercialise and scale Carbon Capture and Utilisation industrial processes to make low-carbon and carbon-negative construction materials. Our first market-ready products are Breathaplasta and Breathaboard, which are drop-in alternatives to standard materials such as plaster and plasterboard, respectively. Working to be ecologically regenerative and economically profitable, Adaptavate is building a business that doesn’t take from the planet but is part of the planet. The combination of large-scale industrial processes and widely used products result in significant potential for carbon removal on a global scale. For more information, please visit: www.adaptavate.com.
NOTES
Breathaboard has a saving of approx. 4 Kg CO2 equiv. of GWP per m2 (compared with a standard board from one of the main players in the UK plasterboard market), when measured using the standard defined by EN 15804 +A2 and counting the biogenic storage of our bio aggregate (3 Kg/m2). All calculations are developed through an Adaptavate proprietary tool which has been independently verified by the Building Research Establishment (BRE) Group. This tool not only calculates GWP but all 28 environmental, energy and resource use parameters for in use impacts.